
Our Technology Glossary.
Heat Pumps.
Naturally, heat moves from a higher temperature to a lower temperature. What a heat pump does is reverse this process using some simple science that takes outside heat energy, via the ground or air, warms it up and then feeds this into your house.
The simplest explanation that addresses this process nicely is the old adage that a heat pump is like a fridge working in reverse. However, if you want to go one step further and understand the processes in more detail then take a look at this link below for a simple guide.
In an air source heat pump (ASHP), the heat is extracted from air passing past the outside unit (making the location of the heat pump an important consideration to ensure enough air flow). Within the system a refrigerant carries the absorbed heat which is then compressed within the pump and increased. This useful heat is then used to heat water that feeds into radiators and the cooled refrigerant is pumped round the system to start the process again.
In an ASHP there are two set up options which are Monobloc or Split. Both do the same thing but within the Monobloc all the kit is located outside in a larger unit (so the extraction and compression of heat occurs in the same place) whereas in a Split system you will have an outside unit and an indoor and the process is ‘split’ between these two units. The indoor unit has a similar appearance and footprint as a typical boiler so will look very familiar to tenants.
Ground source heat pumps (GSHP) work slightly differently and extract the heat from the ground outside, which is a more stable temperature, or from a body of water. However, the process is very similar and heat gathered from the outside is compressed and increased before being released into the home. This makes the heat pump a very efficient way of heating a home.
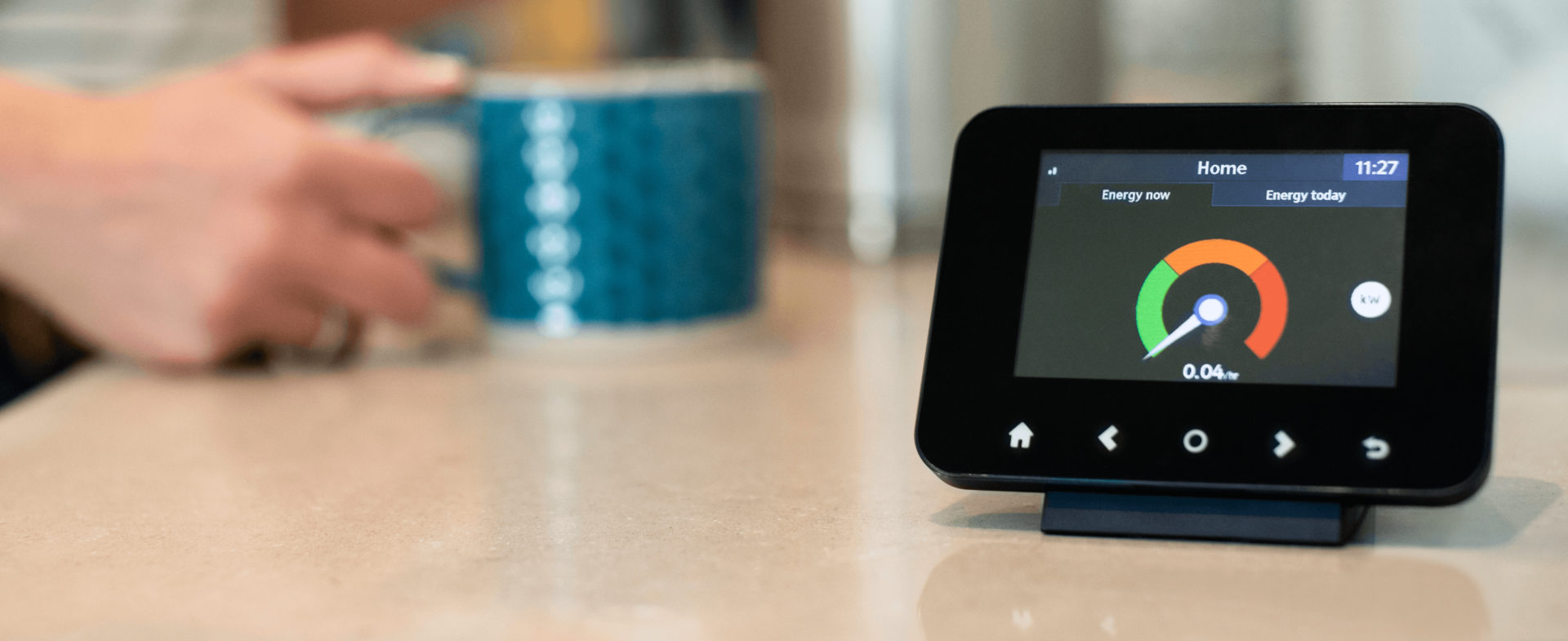
Insulation
Insulation works by slowing the heat loss from the building by creating a barrier between two areas that differ significantly in temperature – e.g. the inside and outside of your house. Houses can lose a lot of heat with up to 30% being lost through the walls and 25% from the roof. This means that walls and roofs, as well as windows, doors and floors, are the most important areas to ensure are insulated. Insulation can take many different forms depending on where it’s going to be located. These include rigid boards made of set plastics or semi-rigid batts and quilts made of more fibrous materials such as mineral or sheep’s wool. As there are lots of places a dwelling can lose heat, there are also lots of different locations to apply insulation. Here’s a look at some of the main ones:
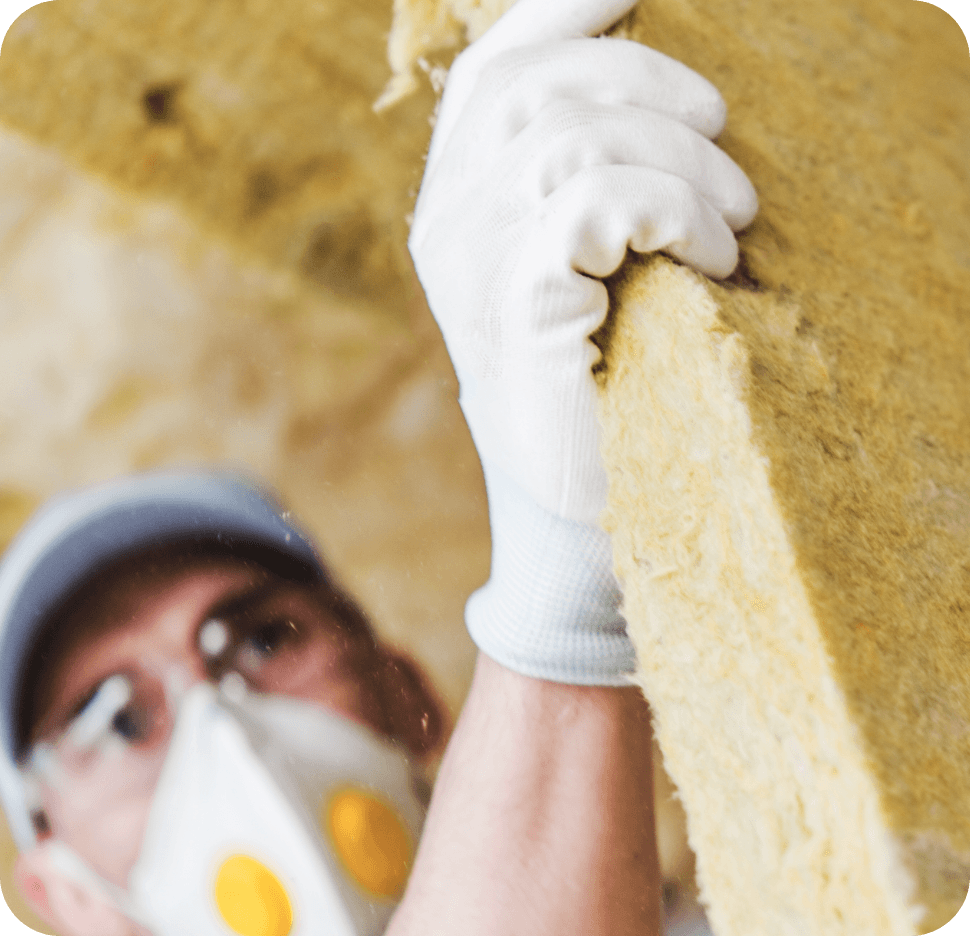
EWI
External Wall Insulation is where insulation is placed on the outside of a property. This is commonly installed on solid wall constructed properties – those without a cavity – but it can be done on many types of property. As it is exposed to elements this type of insulation needs to be weather resilient. Rigid boards are typically used for EWI with a weather protecting render/brick slip applied on top.
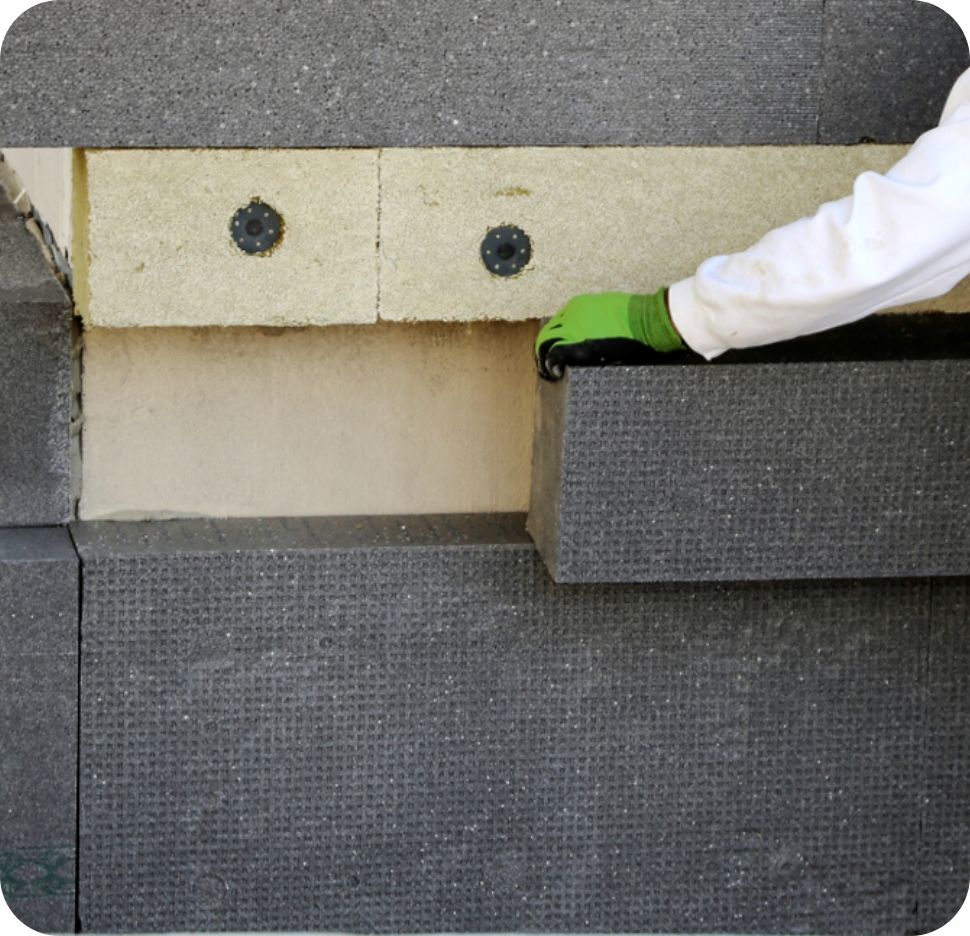
CWI
Cavity Wall Insulation is installed on properties built with a cavity – typically properties built after 1920/30s. There are a few main materials used for cavity wall insulation including blown mineral fibre, polystyrene beads of expanding foam, what’s most appropriate will depend on the type of home you’re looking to insulate. The chosen material is ‘blown’ into the cavity space through drilled holes until it is filled. Once filled, if done properly, this is a no-regret fit-and-forget solution.
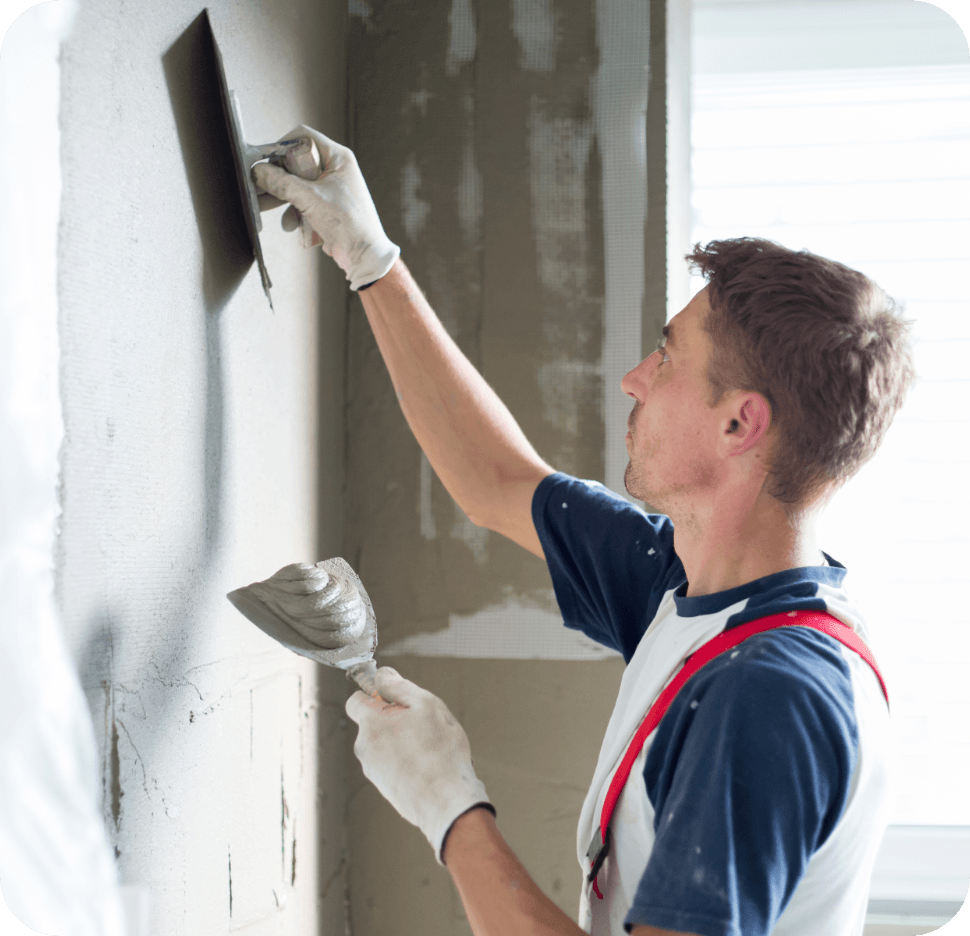
IWI
Internal Wall Insulation is installed on the, you guessed it, interior side of the walls. This is again a common form of insulation for solid wall construction. Rigid boards or semi rigid batts are common materials for IWI these are fixed to the walls or placed between battens, respectively. Plaster and decorative finishes are then applied to the wall.
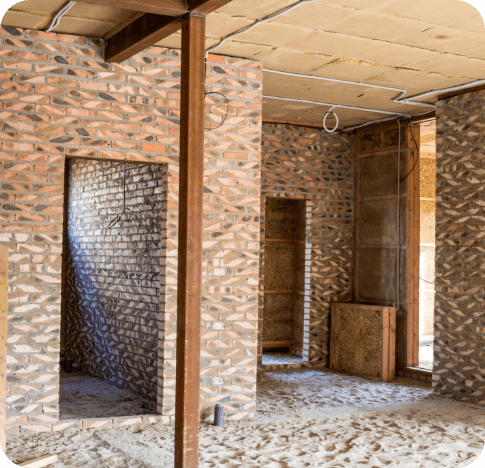
Loft
Loft insulation is a relatively easy and common solution in the UK. This involves rolling insulation quilts between the joists and then cross-laying further rolls of quilt on top of this to reach the recommended thickness – up to 350mm. Loft hatches should also be insulated to avoid thermal bridges. This is known as a cold roof as the insulation is above the ceiling and the space above is cold.
It is important to ensure there is appropriate ventilation maintained within the loft space and, should the space be used for storage, loft boarding will be required to ensure the insulation is not compressed which will reduce its effectiveness.
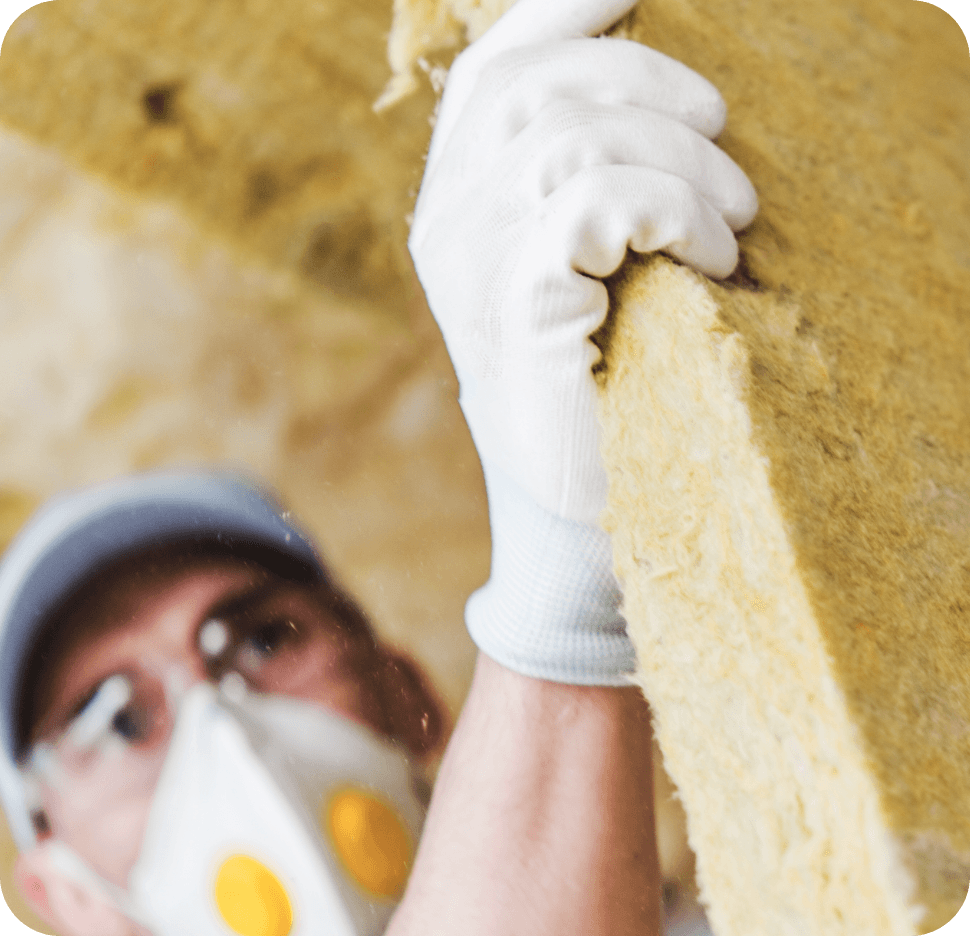
Roof
With roof insulation, rather than between the joists, insulation is placed between the rafters in a pitched roof creating a ‘warm’ roof space. The materials used for this can be rigid or semi-rigid batts and an additional layer can be added fixed below the rafter insulation to further increase the U-values.
Flat roofs can also be insulated and can, again, create ‘cold’ or ‘warm’ roofs depending on where the insulation is placed. A warm flat roof is where the insulation sits above the structural roof deck and below the waterproofing, in between and above the rafters. In comparison a cold roof is where the insulation sits above the ceiling level but between and below the rafters leaving a cold space above. Warm flat roofs are generally viewed as the preferred flat roof solution.
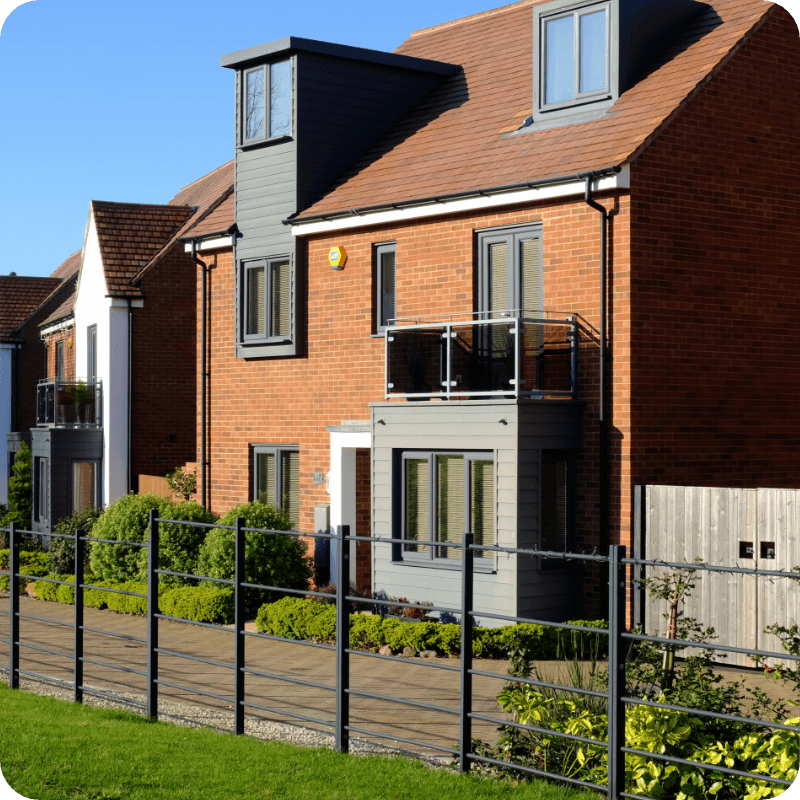
Room-in-Roof
Room-in-roof insulation combines the elements of IWI, loft and roof insulation and needs to take into account the different heat loss elements involved such as the sloped or flat ceilings, stud walls, dormer and gable walls. The processes for roof, loft and internal wall insulation will be combined as part of the process and care needs to be taken to ensure that thermal bridges are avoided at corners, junctions and any remaining loft space is insulated appropriately as well.
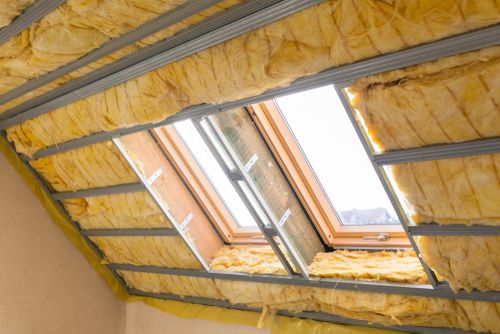
Floor
Dwellings can lose up to 20% of their heat through the floor so ensuring these are well insulated is an important part of retrofit. When insulating floors one of the biggest considerations is how it will affect the ground level in relation to doors, staircases and plugs as adding a layer of insulation can raise the floor height – though this is more of a problem for a solid floor installation. In all cases, installation of floor insulation does also allow for exploring if underfloor heating could also be incorporated into the project, minimising future disruption and return visits. Likewise, floors should always be assessed to see whether they are structurally sound before progressing with insulation.
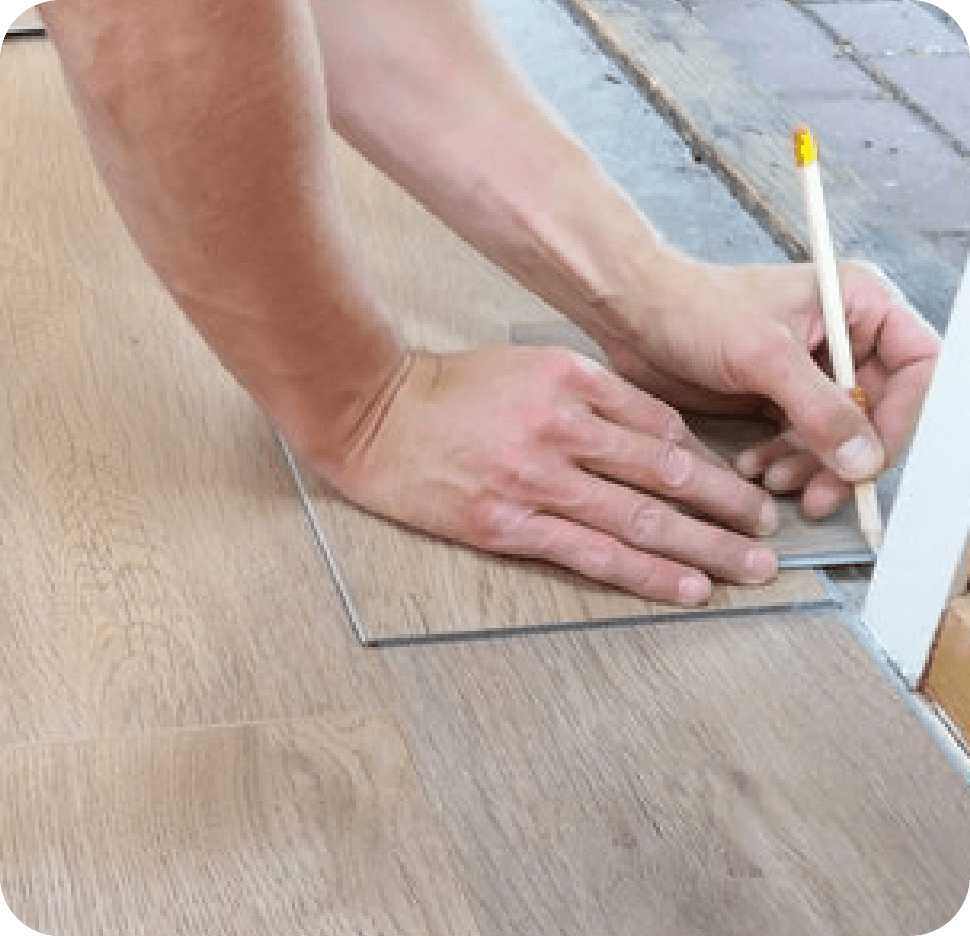
Suspended
Various materials can be used for suspended floors including rigid batts, mineral wool or even sprayed foam. Insulation is placed between the joists and held in place with wooden batts, nails or straps. Any gaps should be sealed to avoid draughts.
In places where the void under the suspended floor is very tight, companies such as Q-bot have created a solution where sprayed foam is delivered via a robot either entering through the airbrick or a small entry space cut into floorboards.
Floor void ventilation needs to be maintained at all times.
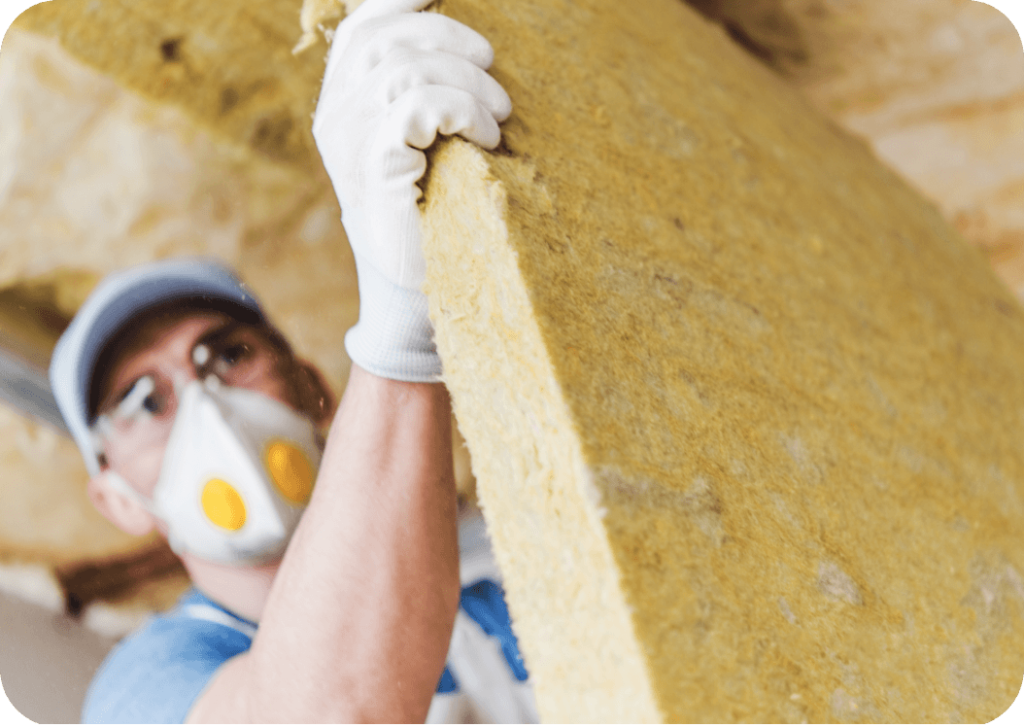
Solid
With solid floors, there are two main options. A ‘floating’ floor can be installed on top of the existing floor. This is when you will have to be aware of increasing the floor level and how this will impact features in the home, especially doors and staircases. Insulation is laid on the existing floor and a floor finish placed on top.
In some cases the existing floor will need to be replaced and a newly insulated floor laid. This will involve breaking up the existing floor, removing from site and then laying a new concrete floor, insulation and a new floor finish. This is a much more disruptive option and the impact on tenants should be considered.
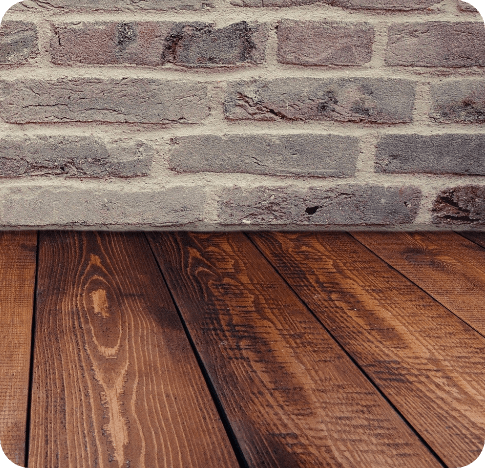
Solar Panels
Solar panels are a renewable technology that generate electricity using the sunlight. The electricity created by solar PV panels is direct current (DC) and cannot be used to run household appliances directly and requires an inverter, a core part of a solar panel system, to convert DC electricity to alternating current (AC).
To get the optimum energy production a South facing roof is considered the best, however East and West can also work well and produces a generation profile that more closely matches the electrical consumption of a home. Considerations should be given to the amount of shading from trees and tall buildings as well as the roof angle to get the best from panels.
Installing solar panels across your stock is another low regret option as it doesn’t adversely affect other retrofit solutions and, as everyone uses electricity, can help every suitable house.
Solar storage is another way to maximise the consumption of energy as the profile of when the sun is shining at its strongest and the panels creating most electricity typically doesn’t match the energy consumption profile of the average household. Batteries installed alongside solar panel systems can store the produced energy for when the household requires it. Batteries are now being trialled as a means of generating revenue for landlords as they can offer energy network management services by powering up or down as the grid requires – like seen in the HaES project!
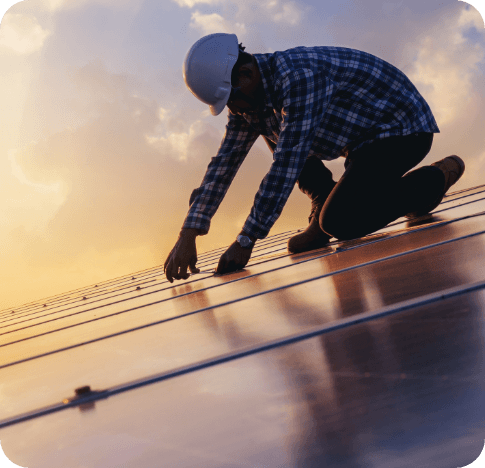
To get the optimum energy production a South facing roof is considered the best, however East and West can also work well. Considerations should be given to the amount of shading from trees and tall buildings as well as the roof angle to get the best from panels. Solar storage is another way to maximise the consumption of energy as the profile of when the sun is shining at its strongest and the panels creating most electricity typically doesn’t match the energy consumption profile of the average household. Batteries installed alongside solar panel systems can store the produced energy for when the household requires the energy.
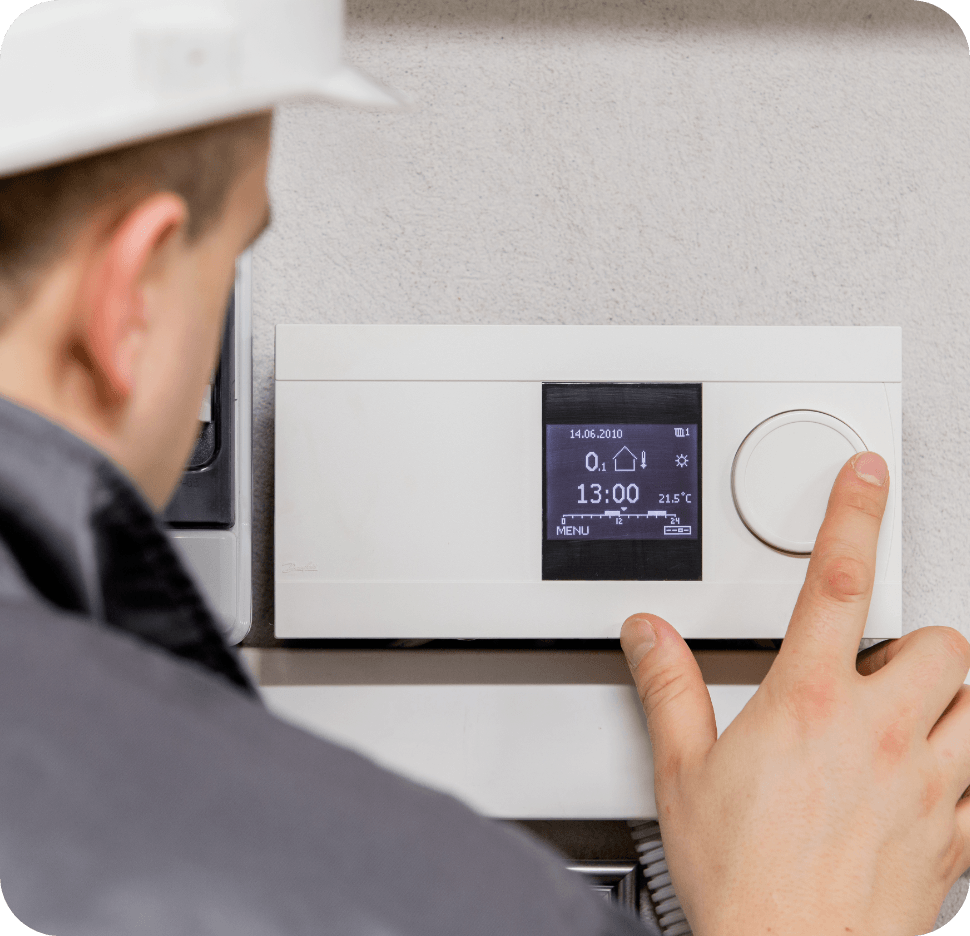
Solar Thermal
Solar thermal uses the suns energy again but instead of electricity, heat is captured through evacuated tubes or ‘flat plates’ that form a panel called a solar collector. The generated hot water is stored in a domestic hot water (DHW) cylinder. This is a good solution where properties have a very high hot water demand and will reduce the amount of gas or electricity needed to provide water which will also save carbon and money. It is also possible for solar thermal to contribute to space heating as well.
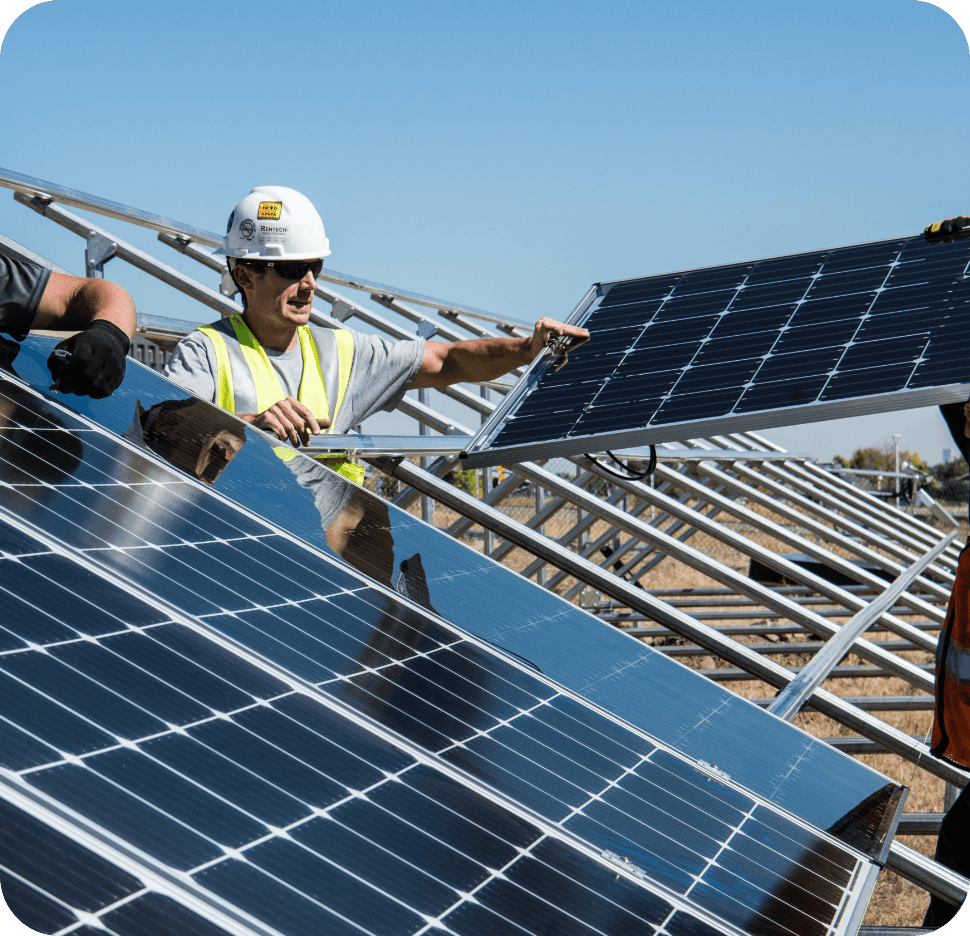
Solar PV-T
Solar PV-T is a combination of a traditional solar PV panel and solar thermal solution into one module. These are a newer technology and so the supply chain is less developed. It could be a good solution for smaller roofs that wouldn’t have space to install both solar PV and solar thermal panels.
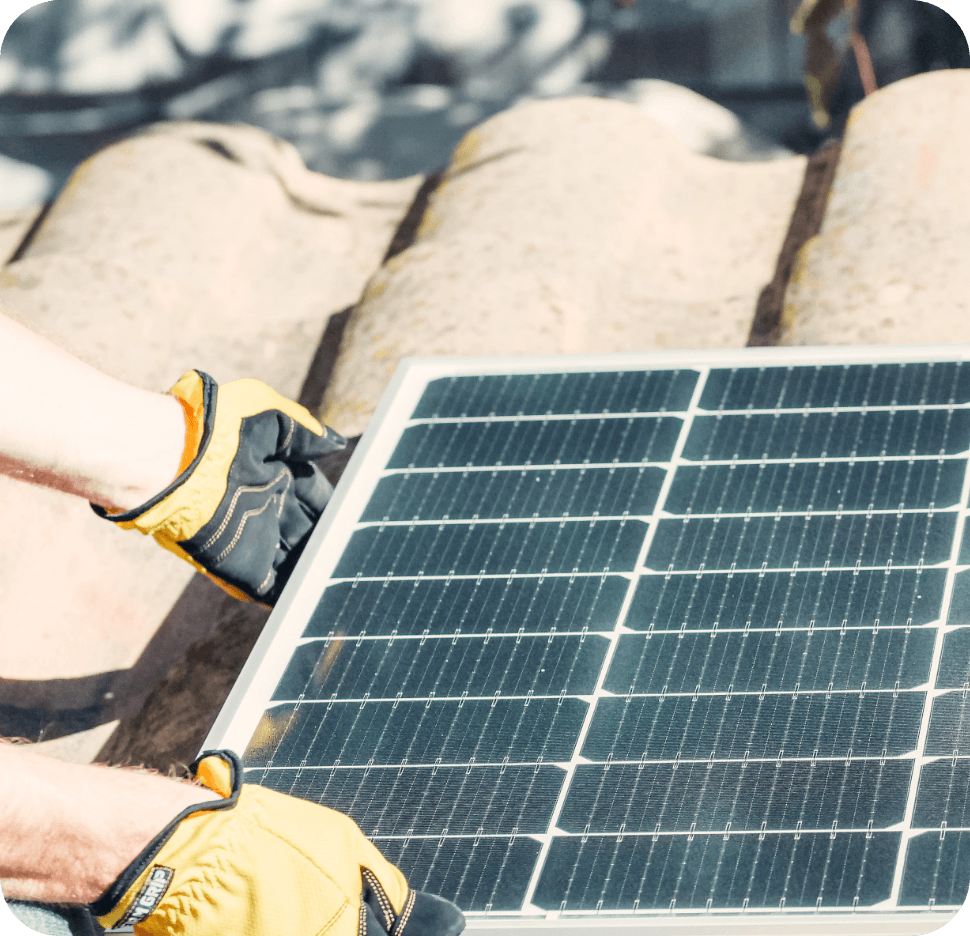
Ventilation
Ventilation is an incredibly important element of retrofit that is often overlooked and failure to ventilate properly can, in the extreme, cause serious health issues as well as leaving homes uninhabitable.
Ventilation is the process where ‘stale’ polluted air from inside the buildings is removed and replaced with ‘fresh’ external air (which is usually less polluted). One of the key pollutants in the home is the build-up of moisture caused by occupants breathing, showering and cooking. This can lead to condensation and mould growth.
When retrofitting properties the goal is to ensure there is purposeful ventilation, that is to say ventilation that is designed into a property rather than unintentional – as is seen in older, draughty buildings. With properties nowadays being made more air-tight, more care must be given to the ventilation requirements and the maxim ‘build tight, ventilate right’ is an important one to remember!
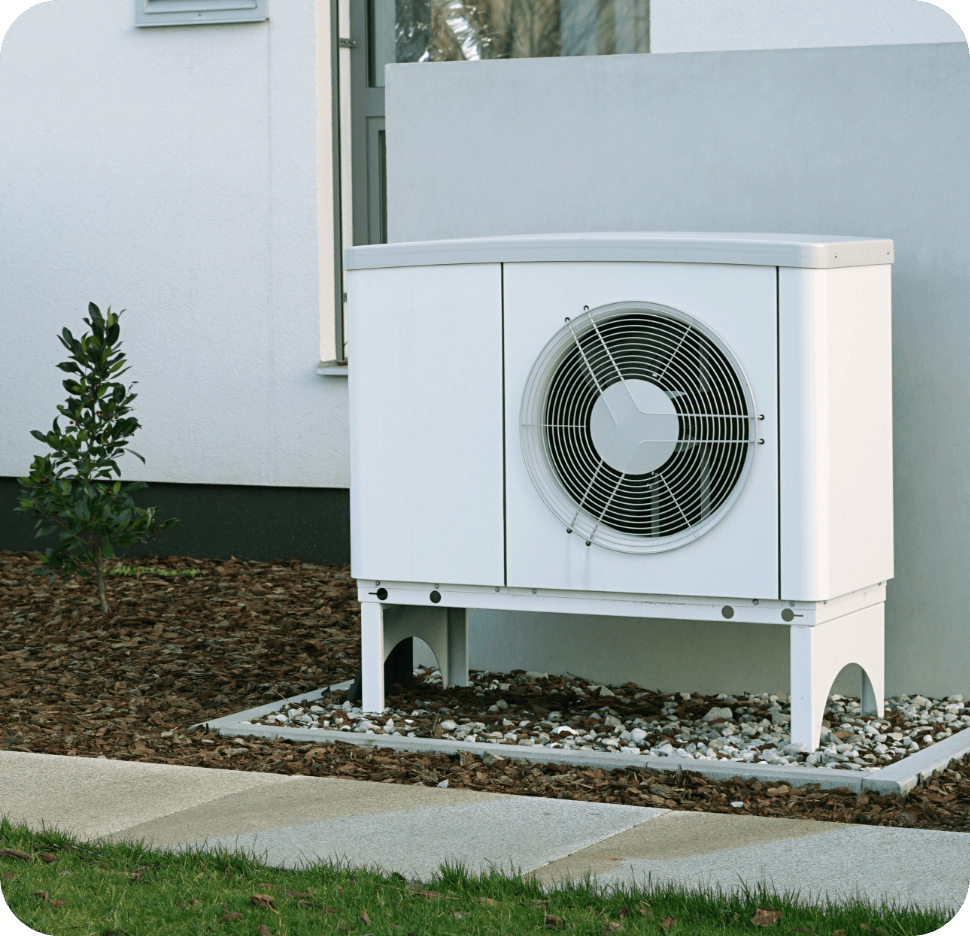
Intermittent Extract Ventilation (IEV)
IEV systems are a common basic ventilation solution where multiple individual extractor fans are placed in all wet rooms like kitchens, bathrooms, utility rooms and toilets. These can be set for continuous or intermittent operation as required. Background trickle vents allow fresh air into the property. IEVs are quiet running, come in compact designs and have a low energy usage meaning a low running cost.
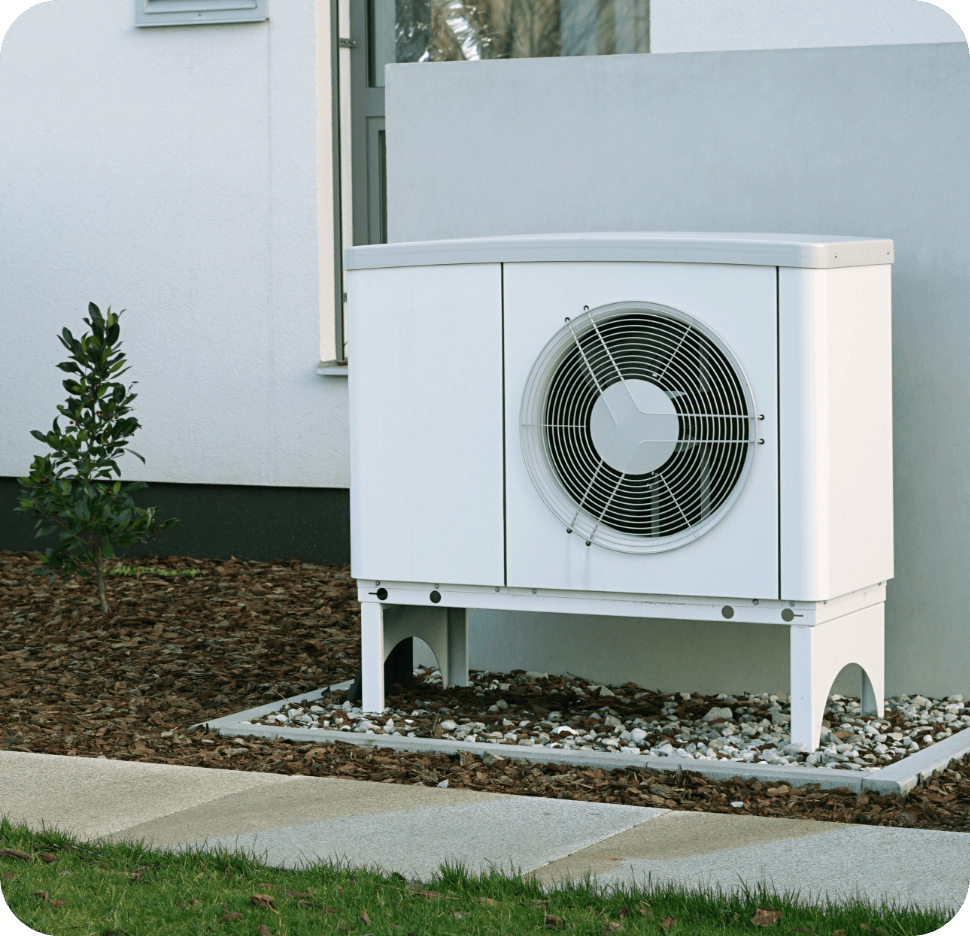
Mechanical Extract Ventilation (MEV)
MEV systems are similar to individual extract fans except that each area is connected by ducting to a single extractor fan located remotely (typically in a loft space) and the air expelled from one outlet. It is designed to work continuously at a low level in the background but can be boosted when required.
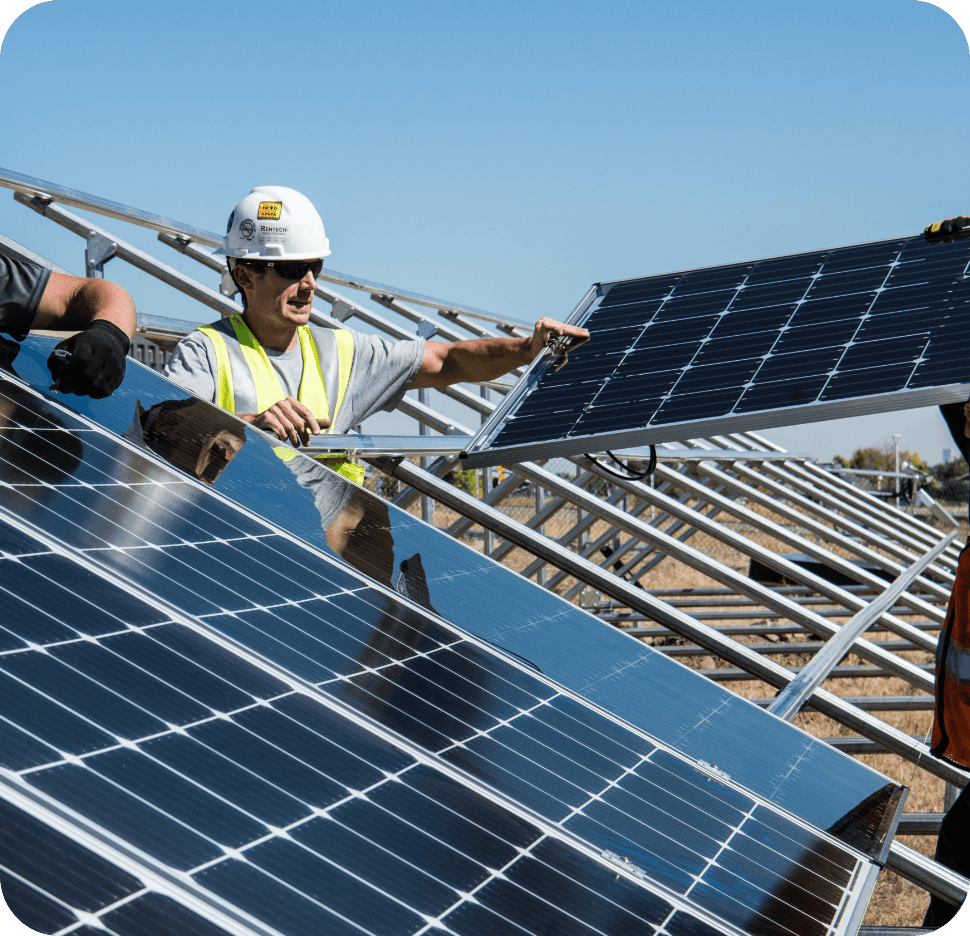
Mechanical Ventilation with Heat Recovery (MVHR)
MVHR is a continuous source of ventilation that extracts stale, moist air from a building and resupplies fresh, filtered air back in. It works by extracting the air from traditionally ventilated wet rooms, this moist air is passed through a central heat exchanger and the heat recovered. This heat is used to heat the fresh air that is coming into the property to supply warm, fresh air to the ‘habitable’ rooms (bedrooms, living rooms, studies etc). If the inside air temperature is cooler than outside the fresh air will be cooled instead, maintaining a comfortable temperature in the property.
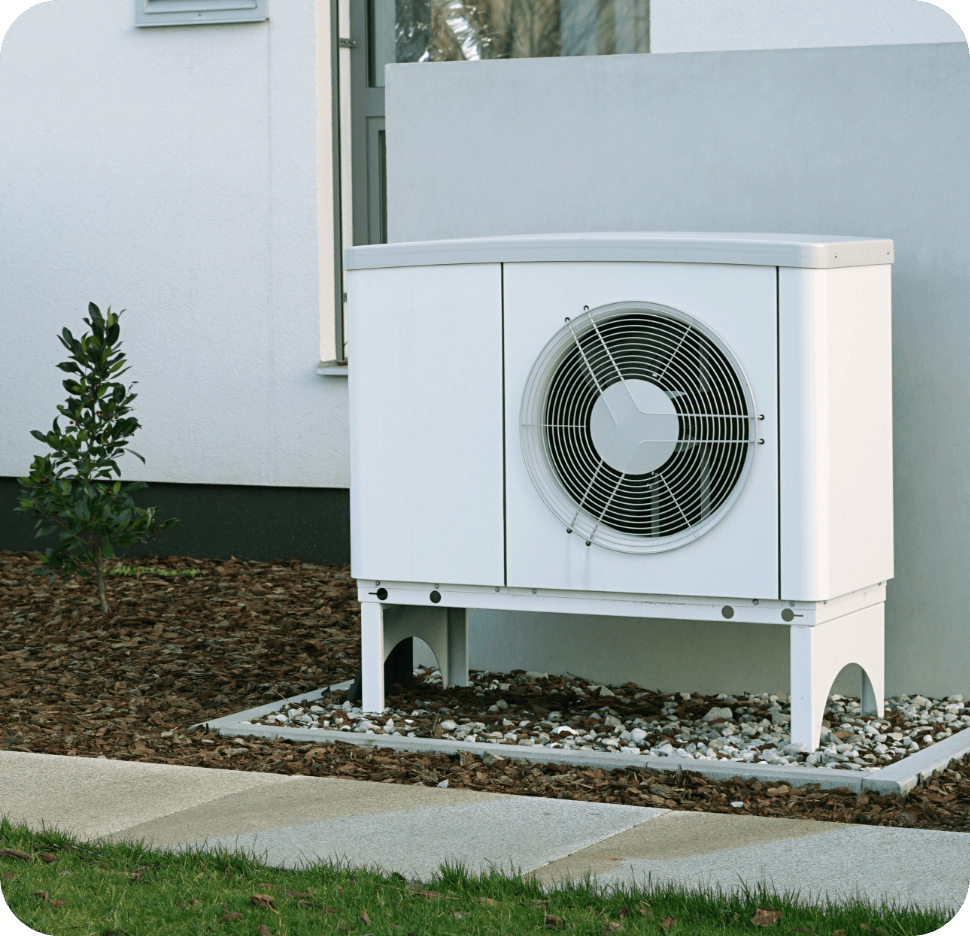
Single Room Heat Recovery Ventilation (SRHRV)
SRHRV systems are effectively decentralised versions of an MVHR system dedicated to a single room. If not wanting to go for a whole house solution, a SRHRV is a good replacement for traditional basic room-by-room ventilation systems.
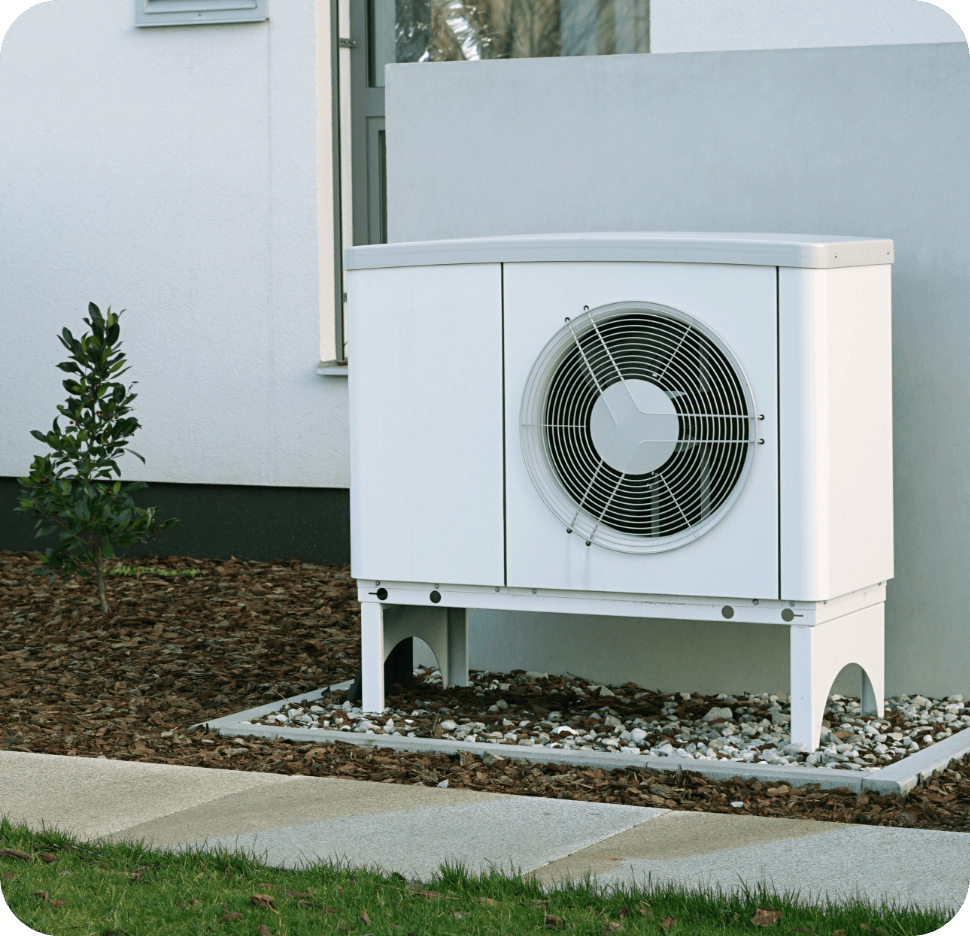
Passive Stack Ventilation (PSV)
PSV is a natural, non-mechanical intervention for providing ventilation to a home. It brings fresh air into the building through vents and gets rid of stale air using the ‘stack effect’ which is the movement of air due to differences in temperature between inside and outside as well as the effect of wind moving across the roof of the house. Ducts are installed leading to roof vents that expel the warmed wet air while fresh air is allowed in through trickle vents in the windows and walls. It is a cost effective solution as there is no mechanical requirements.
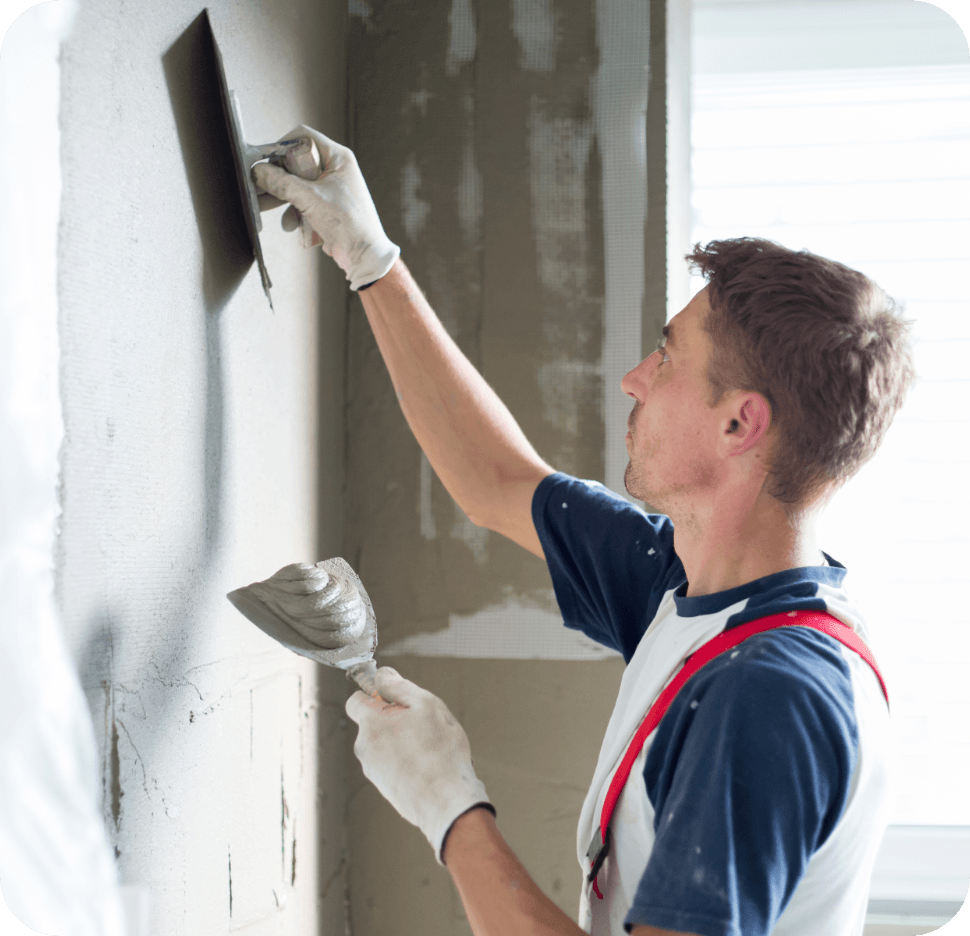
Demand Controlled Ventilation (DCV)
DCV is a ventilation solution that manually or automatically regulate the airflow to meet the exact need at a given time. If a room is empty, supply of air is reduced and if another room is full of people, the system will increase the volume to this area. DVC regulates based on temperature, air-quality, humidity and occupancy meaning it delivers what is needed and can be an energy and cost saving mechanism. The footprint of DVC systems is similar to traditional extractor fans.
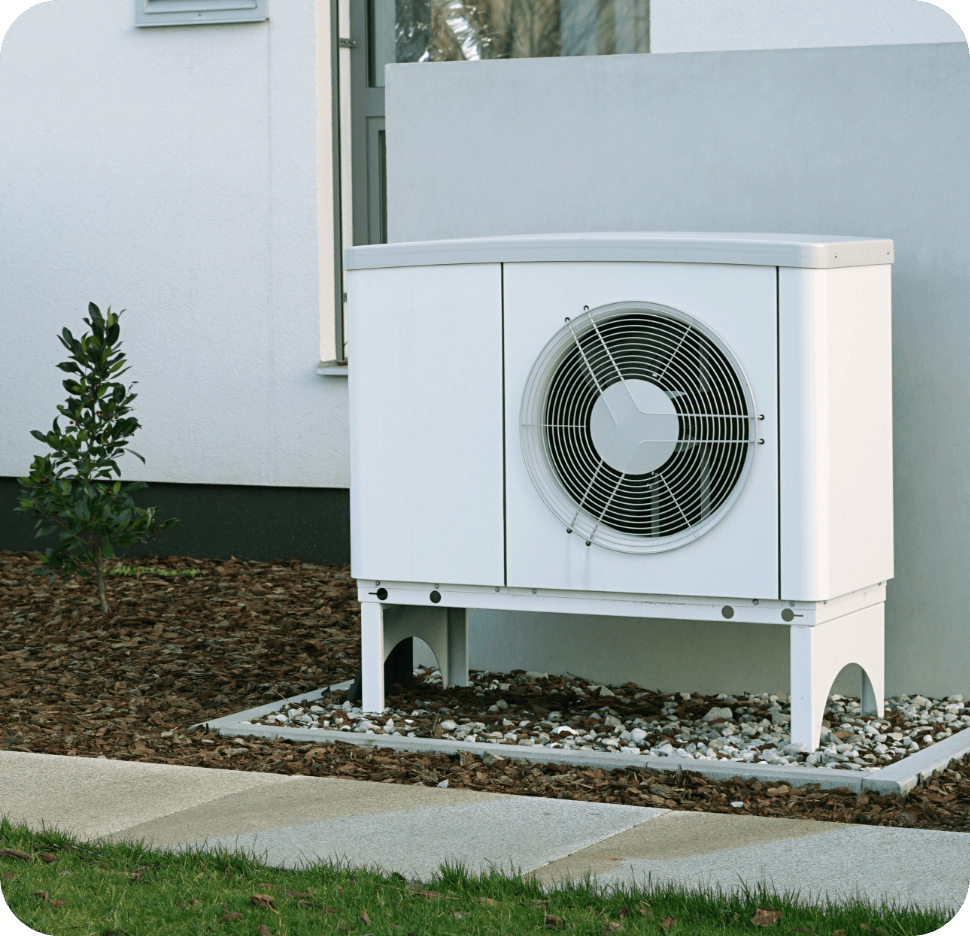
Glazing
Window glazing is another common retrofit measure and there are options for most window styles including traditional sash or casement windows.
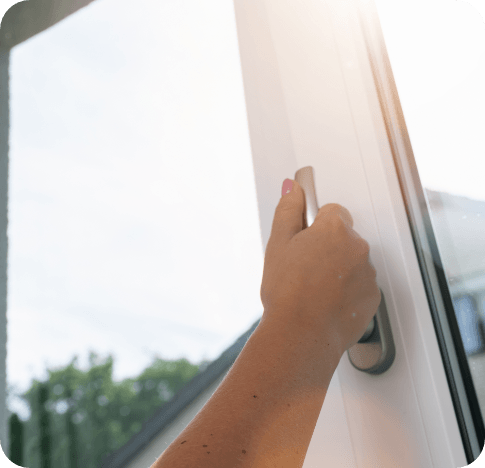
Double
Double glazing refers to the use of two panes of glass in a window with a gas, such as argon, between the panes to act as an insulator. It can reduce heat loss from the windows as well as noise pollution.

Triple
Triple glazing involves three panes of glass separated by gas and so is an extra layer to insulate your home over double glazing. Triple glazing is, however, substantially more expensive than double glazing whilst the U-value gains are not as significant. It is worth doing a cost-benefit analysis when looking at choosing between double and triple glazing.
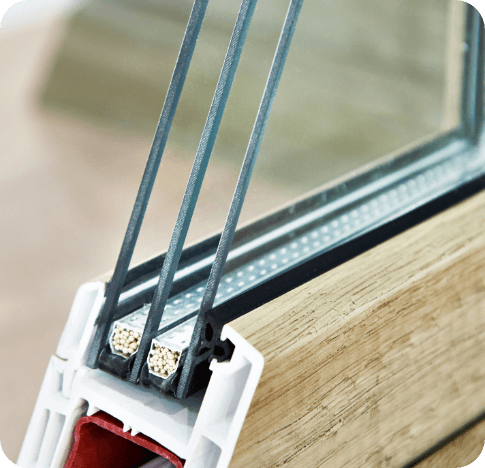
Vacuum
Vacuum glazing is very similar to a double glazed unit in terms of construction with the difference being instead of gas between the panes there is a vacuum – essentially a layer of nothing. This can be much more effective at insulating a house than standard double glazing. As the vacuum requires a much smaller cavity the thickness of the windows is also reduced.
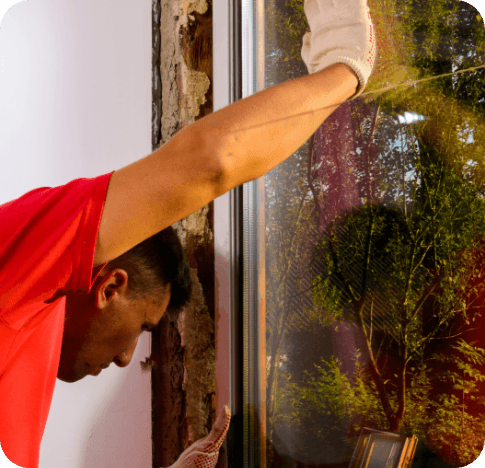
Important Low Carbon Terms
Important Low Carbon Terms
PAS2035
While not a technology per se PAS2035 is very important to be aware of and has been introduced to combat shortcomings in the domestic retrofit industry which has, in many previous cases, been delivered poorly without a true understanding of the occupants needs, the building physics and the goal of ensuring homes in the UK are healthy, warm and comfortable while reducing energy consumption.
What is it?
As above, the failures of the retrofit market led the UK government to commission the Each Home Counts review in 2015. One of its recommendations was the establishment of an industry-wide Code of Practice which has resulted in the publication of PAS2035.
PAS2305 is an overarching framework and process guide for delivering retrofit. It is about managing the process of how retrofit is delivered ensuring the correct people with the right qualifications are undertaking each stage. For publicly funded works it is mandatory that projects are compliant with PAS2035 and for any installer that claims to be TrustMark registered it is compulsory to follow the process. In the private market, this is a voluntary code to be followed but it is highly recommended property owners and private landlords adhere to the standard.
PAS2035 promotes a ‘whole-house’ or ‘whole-building’ approach for retrofit meaning that energy efficiency or renewable technology measures need to be considered as part of a package for the property that can be delivered all at once or over a number of stages.
Who is involved?
PAS2035 sets out 6 distinct roles and details the qualifications that are required by each. It is not necessary that all the roles are carried out by separate individuals but anyone carrying out more than one title in the project will need to make sure they have the appropriate qualifications to deliver that role.
Retrofit Advisor – delivers advice to clients / householders
Retrofit Assessor – undertakes retrofit assessment
Retrofit Coordinator – essentially the retrofit project manager
Retrofit Designer – undertakes the design
Retrofit Installer – installs scheme based on retrofit design
What is the process?
Setting the intended outcomes
Here the Retrofit Advisor will discuss with the Client – property owners/landlord/occupants about what they want to achieve from the retrofit and will capture this in the form of an Intended Outcomes Statement
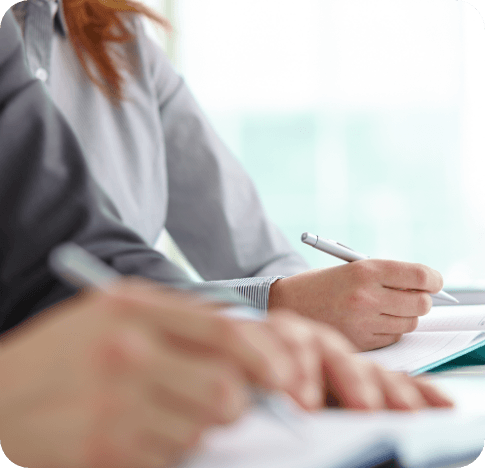
Risk Assessment
The Retrofit Coordinator will identify how risky the project is depending on how big the project is or what measures are expected and this will inform who will need to be involved (and what qualifications they’ll need) to produce the specifications for the measures / complete the rest of the PAS2035 roles. This stage ensures you have an appropriate team for the complexity of the project.
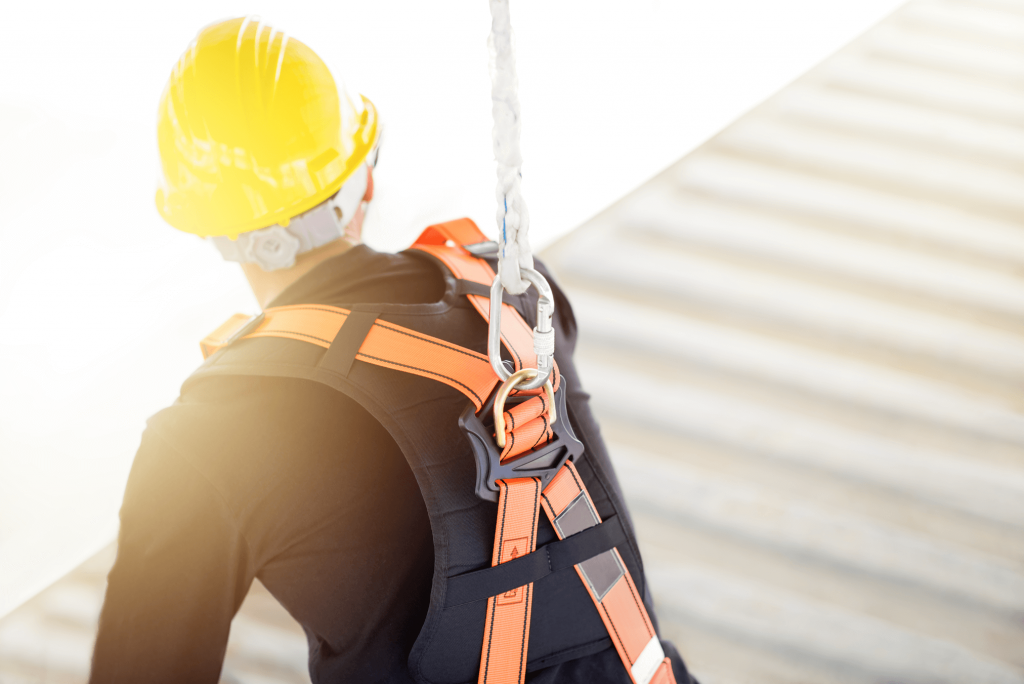
Whole House Assessment
The Retrofit Assessor will look into what’s there now, what can be kept, what needs to be changed and what could be installed to meet the intended outcomes. Importantly this looks at the ventilation currently within the property. From this a list of likely measures is developed and dependent on the risk path will lead to an options appraisal and the creation of a medium term improvement plan.
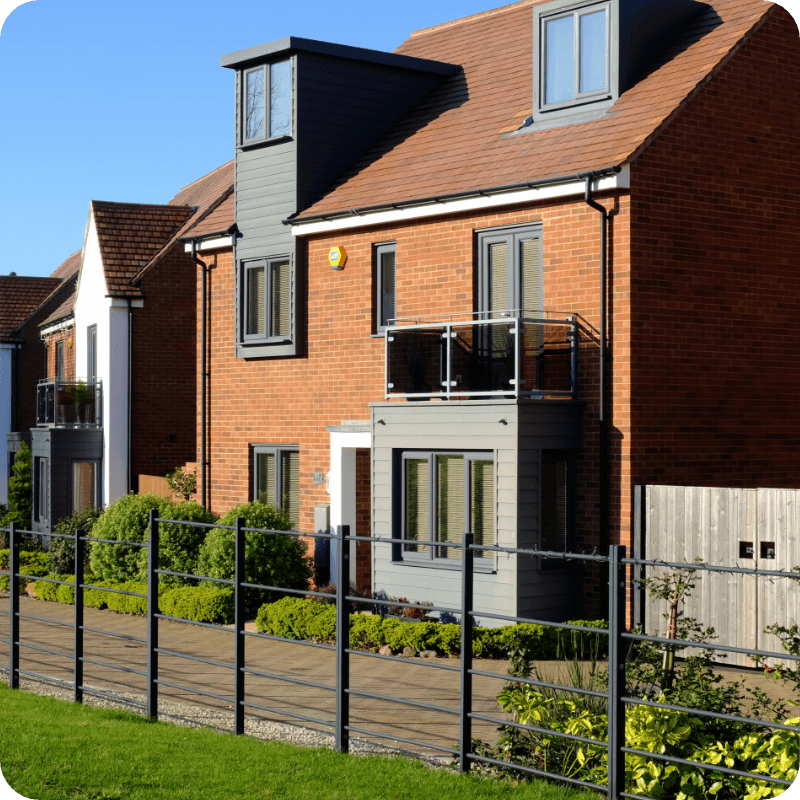
Design
Delivered by the Retrofit Designer this is a detailed, dimensionally accurate and materially accurate representation of what and how the measures will be installed.
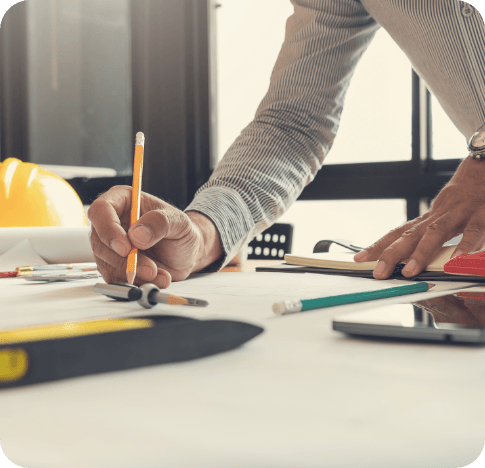
Installation
Here is the familiar part of retrofit – the installation. PAS2035 stipulates that for Retrofit Installers need the appropriate certifications, for renewable technologies this means they will need to be MCS certified and any fabric measures they will need PAS2030:2019. Retrofit Coordinators are involved here to check installers are working to the correct standards.
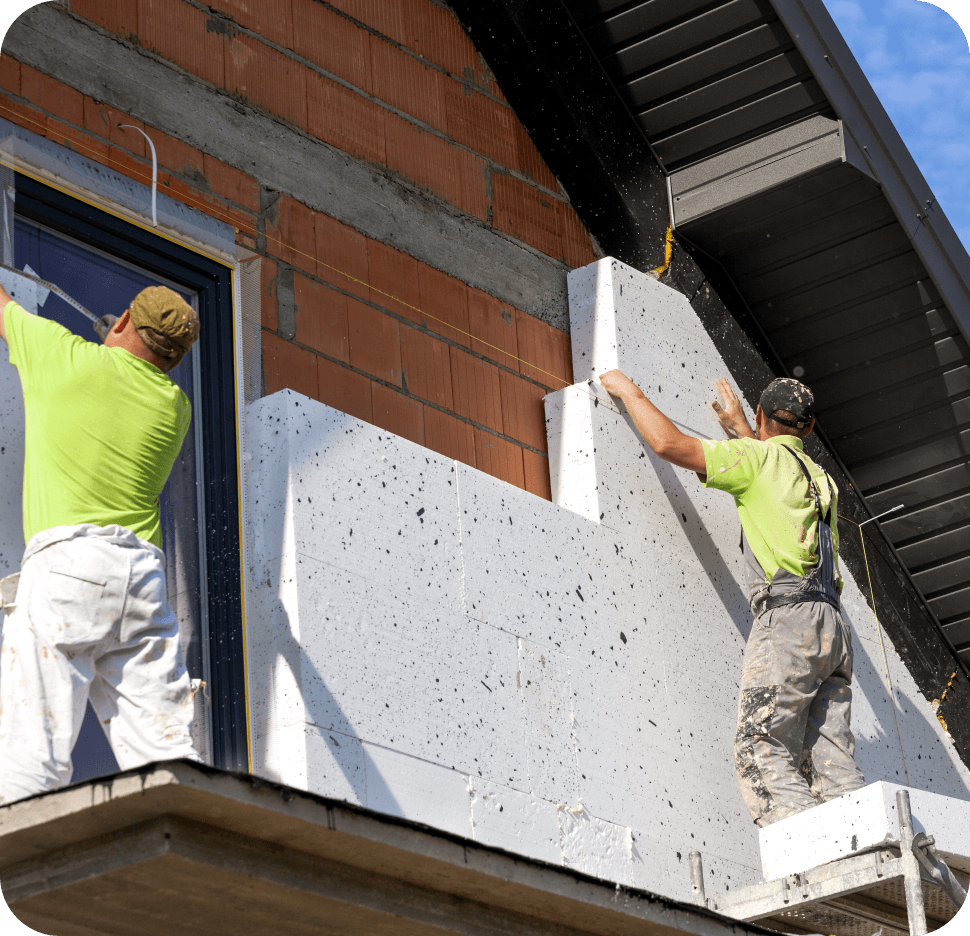
Monitoring and Evaluation
This is undertaken by the Retrofit Evaluator and the monitoring and evaluation should be done to understand if the objectives set in the intended outcomes have been achieved. If the evaluation draws attention to any problems, these will need to be rectified.
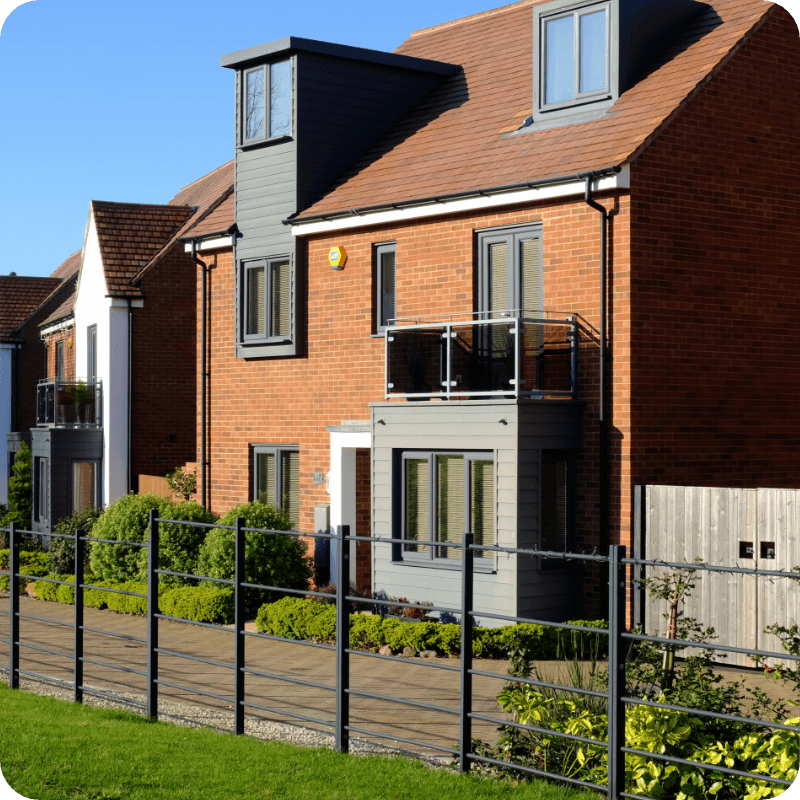
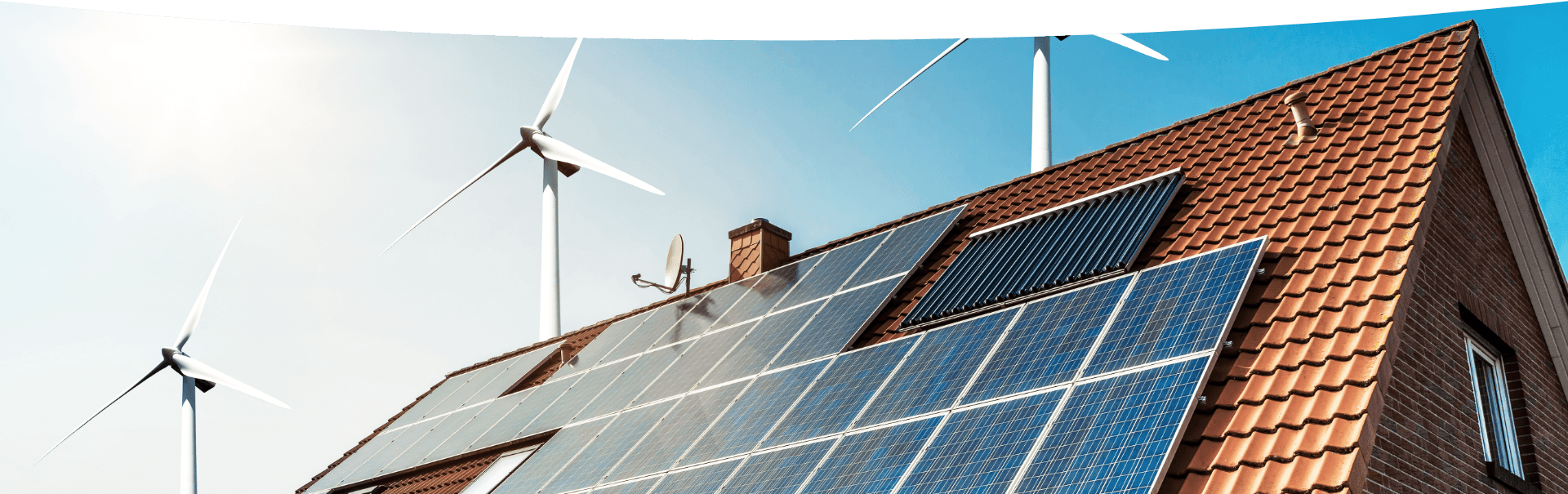
How do you access information or get in touch?